The Fully Automatic Compressed Coal Ball Briquette Production Line is designed for high-efficiency coal briquette manufacturing. It transforms fine coal powder into durable and energy-efficient briquettes. This automated system reduces labor costs while ensuring consistent output. Ideal for industrial fuel production, it enhances combustion performance and minimizes waste.
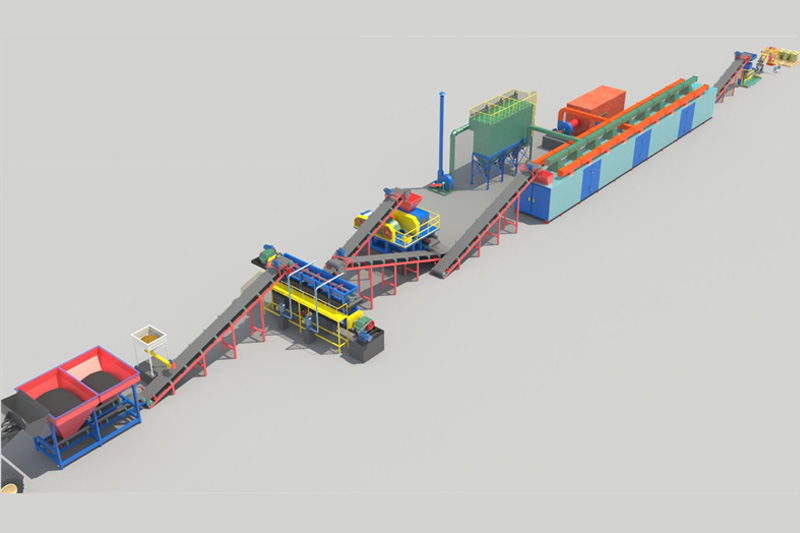
Coal Briquettes Manufacturing Process
Coal Preparation ➝ Mixing & Binders Addition ➝ Briquette Molding ➝ Drying & Hardening ➝ Final Packaging
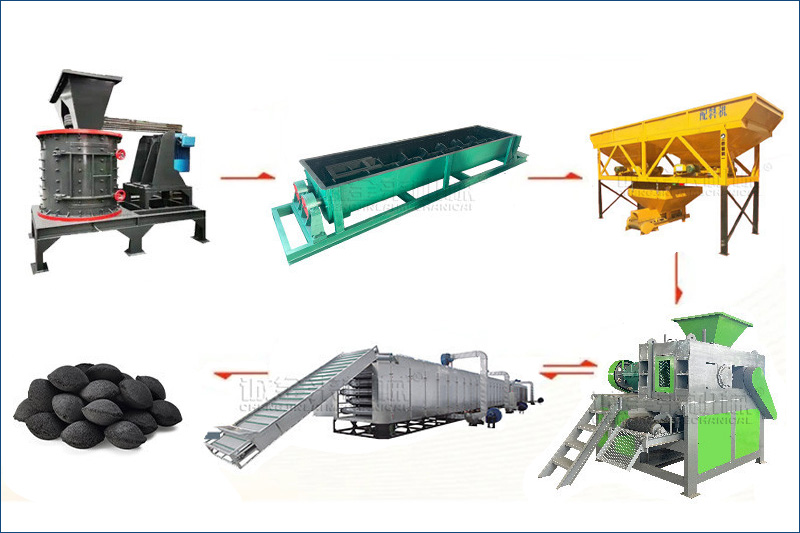
1. Coal Crusher & Grinder
- Function: Crushes and grinds raw coal into fine powder.
- Feature: Ensures uniform particle size for better briquetting.
2. Binder Mixing Machine
- Function: Blends coal powder with water and binders for better cohesion.
- Advantage: Enhances briquette strength and combustion efficiency.
3. Briquette Press Machine
- Function: Compresses mixed material into uniform briquettes.
- Benefit: High-pressure molding ensures dense and durable briquettes.
ball briquette machine Aplication scope: charcoal, clay, coal powder,coal slime,coke powder, mineral powder, manganese ore powder, iron powder.steel slag, desulfurzation gypsum, fluorite powder, dust removal powder,silico manganese ore powder, etc.
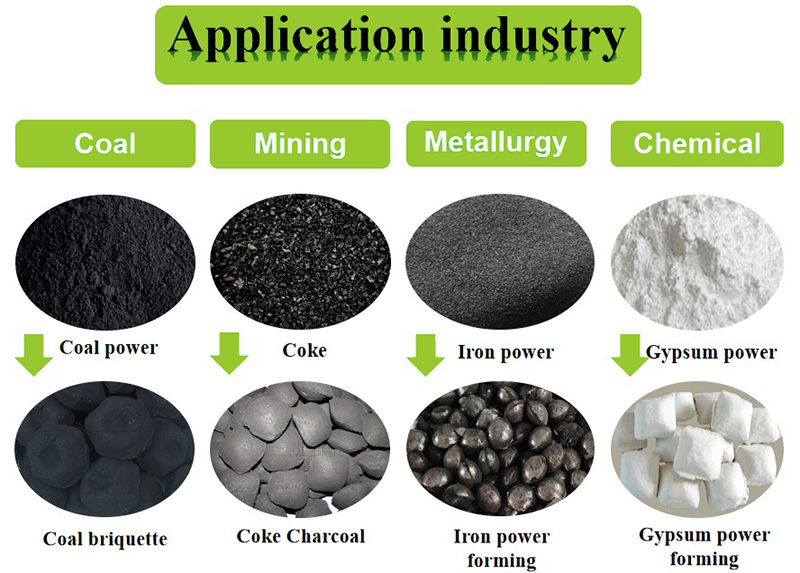
According to customer’s briquette shap request ,we can provide different mould to press the coal powder into different shape such as the following pic display.
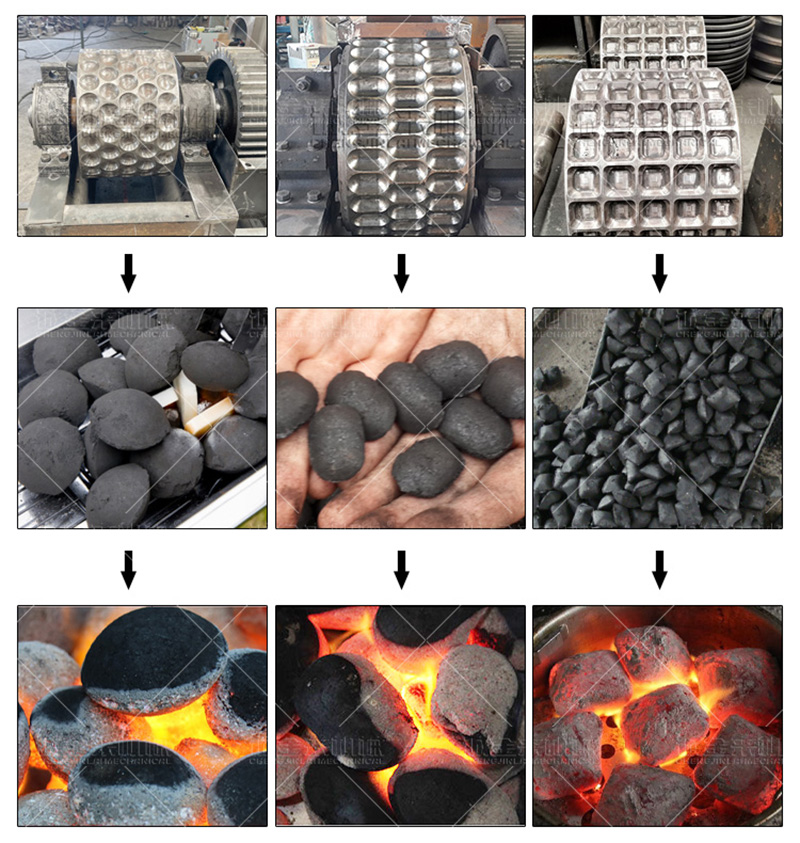
4. Mesh Belt Dryer
- Function: Removes excess moisture from fresh briquettes.
- Feature: Multi-layer drying system ensures uniform heat distribution.
5. Automatic Packaging Machine
- Function: Packs finished briquettes for easy storage and transportation.
- Advantage: Increases efficiency and reduces manual labor.
Coal Powder Press Line Parameter
Briquetting Machine | |||
Model | Capacity(t/h) | Roller Size(mm) | Weight(kg) |
290 | 1-2 | 290×200 | 600 |
Drying Machine | |||
Model | Belt Width(m) | Drying Section Long(m) | Thick material laying(mm) |
CJL-1.2-8 | 1.2 | 8 | 10-80 |
As the above explains our briquette making machine can process different waste dust into different shape through changing the mould, except changing the mould we also supply different briquette making machine type to make the waste dust into different shape.
Coal Bar Extruder Machine
Typical Shapes:Hollow cylinder (honeycomb), Hexagonal prism, Spiral strips
Size Range:Diameter: 10–60 mm (hollow core 5–30 mm)
Length: 100–500 mm (cuttable)
Capacity:220-380kg/h
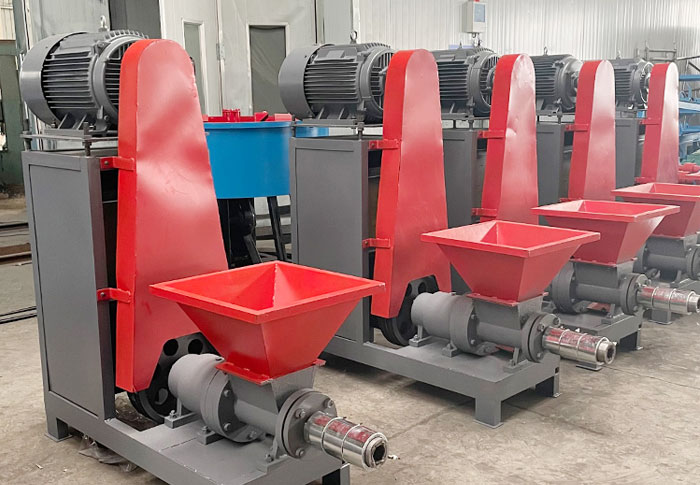
Hydrualic Ball Press Machine
Typical Shapes:Spherical, Porous cubes, Custom relief (e.g. logo)
Size Range:Unit weight: 50–5000 g
Thickness: 10–150 mm
Capacity:0.8-1.0 t/h
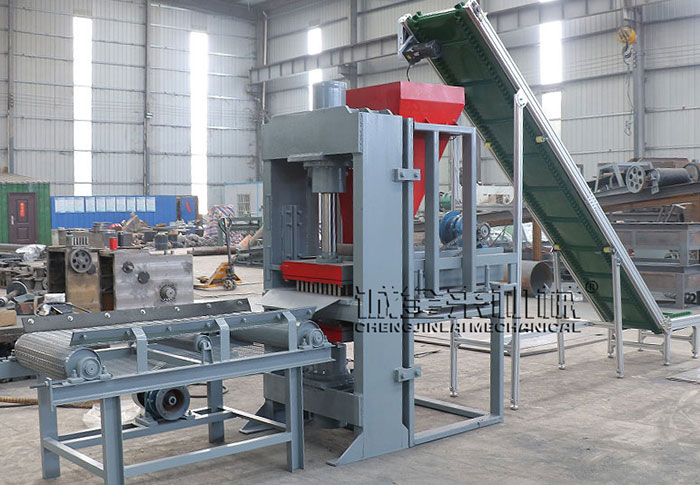
Briquette Production Line Advantages
- Fully automated: Reduces labor costs and increases productivity.
- Energy-efficient: Optimized drying and molding process minimizes power consumption.
- Versatile applications: Suitable for household fuel, industrial heating, and BBQ charcoal.
Benefits
- Stronger briquettes: High compression ensures durability and longer burn time.
- Eco-friendly process: Reduces coal waste and improves fuel utilization.
- Cost-effective production: Low maintenance and operational costs.
Conclusion
The Fully Automatic Compressed Coal Ball Briquette Production Line is the ultimate choice for efficient coal processing. With its advanced technology and automated workflow, it guarantees high-quality briquettes and streamlined production. If you’re looking for a high-performance briquette system, leave us a message today for more details!