What is a rock crusher
Rock impact crusher, also known as vertical shaft impact crusher or sand making machine, is a high-efficiency crushing equipment widely used in the fields of construction sand, ore crushing, etc. The rock impact crusher working principle is to accelerate the material through the high-speed rotating impeller and then throw it onto the rebound plate in the crushing chamber, and the material is crushed by multiple forces such as impact, friction and shear.
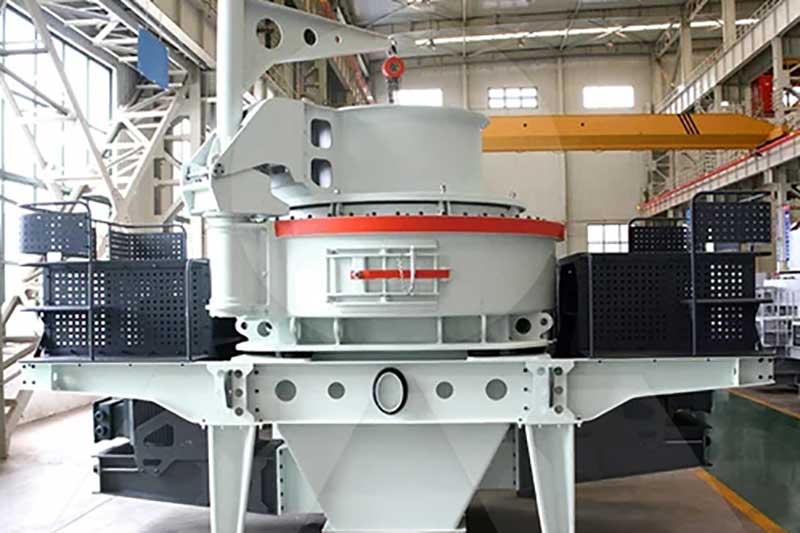
How about the rock crusher working?
Impact crushing. The rock impact crusher uses the impact plate (or hammer head) on the high-speed rotating rotor to hit the rock entering the crushing chamber, causing it to be crushed by huge impact force.
Counterattack crushing. The impacted rock will also collide with the fixed counterattack plate in the crushing chamber during high-speed movement, further crushing.
Grinding crushing. The rock is repeatedly impacted, squeezed, rubbed, etc. in the crushing chamber to reach the required particle size.
How to control the rock impact crusher discharge particle size?
- Adjust the position of the counterattack plate or hammer head. Appropriately reducing the distance between the counterattack plate and the rotor, or adjusting the gap between the hammer head and the crushing chamber wall, can change the particle size of the crushed material.
- Optimize the rotor speed. The crushing effect can be affected by adjusting the rotor speed. A higher speed can increase the number of material crushing times, thereby reducing the particle size.
- Replace severely worn parts. Check the wear of key parts such as hammers and impact plates, and replace new parts when necessary to ensure the crushing effect.
- Control the feed size. Ensure that the particle size of the material entering the crusher does not exceed the design allowable value of the equipment. Excessive materials will increase the difficulty of crushing and cause excessive particle size.
- Reasonable weighting. Adjust the weight of the rock impact crusher to make the equipment more stable during operation and avoid uneven particle size caused by vibration.
- Strengthen screening. Add one or more screening processes after crushing, and unqualified large particles will return to the crusher for re-crushing until the particle size requirements are met.
- Optimize the feeding method. Feed evenly and appropriately to avoid overload or material interruption and maintain a stable crushing process.
If you want to know more about the rock impact crusher equipment, please feel free to contact our online customer service. We will answer your questions promptly.